CPU (Central Processing Unit) is the core component of modern computers, also known as "microprocessors." For PCs, CPU specifications and frequency are often used as an important indicator of the performance of a computer. The Intelx86 architecture has been in existence for more than 20 years, and the CPU of the x86 architecture has a profound impact on the work and life of most of us.
This article refers to the address: http://
CPU It is the core component of a computer. Computer processing can be divided into two steps:
Data and programs (ie, sequences of instructions) are entered into the memory of the computer. Execute the program from the address of the first instruction, get the desired result, and end the run. The role of the CPU is to coordinate and control the sequence of instructions of the various components of the computer to execute the program in an orderly manner. Therefore it must have the following basic functions:
a) fetch instruction: When the program is already in the memory, first a program is fetched according to the program entry address, and the instruction address and control signal are issued for this purpose.
b) Analysis instruction: that is, instruction decoding. It analyzes the currently obtained instructions, indicates what operations it requires, and generates corresponding operational control commands.
c) Execution instruction: form a corresponding operation control signal sequence according to the "operation command" generated when the instruction is analyzed, and realize the function of each instruction through the execution of the arithmetic unit, the memory and the input/output device, including processing the operation result And the formation of the next instruction address.
Further refinement of its functions can be summarized as follows:
Ability to decode instructions and perform specified actions;
Can perform arithmetic and logic operations;
Can exchange data with memory and peripherals;
Provide the control required for the entire system;
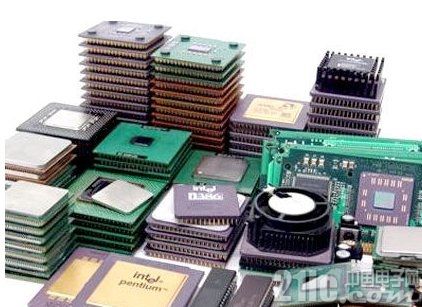
Although the performance metrics and structural details of various CPUs are different, the basic functions they can accomplish are the same. From functional analysis, it can be seen that any CPU internal structure should include at least the following components: arithmetic logic operation unit (ALU), accumulator, program counter, instruction register, decoder, timing and control components.
Many of the friends who know a little about computer knowledge know that the most important thing in the CPU is the transistor, which increases the speed of the CPU. The most important point is how to put more transistors into the same CPU area. The CPU is too small, too precise, and it contains a considerable number of transistors, so the manpower is absolutely impossible to complete, and can only be processed by photolithography.
This is why there are so many transistors in a CPU. A transistor is actually a two-position switch: on and off. If you recall the era of basic computing, it is all that a computer needs to do. Two options, on and off, are 0 and 1 for the machine. So how do you make a CPU? In today's article, we will walk you through the process of a central processor from a pile of sand to a powerful integrated circuit chip.
Manufacturing the basic raw materials of the CPU
If you ask what the raw material of the CPU is, everyone will give the answer easily - it is silicon. This is not fake, but where does silicon come from? It is actually the most inconspicuous sand. It's hard to imagine, expensive, complex, powerful, and full of mysterious CPUs come from the sand that is worthless. Of course, this must go through a complicated manufacturing process. However, it is not a matter of grabbing a handful of sand to make raw materials. It is necessary to carefully select and extract the purest silicon raw materials. Imagine if you use the cheapest and most abundant raw materials to make the CPU, what is the quality of the finished product, can you use a high-performance processor like the one now?
Intel technicians use automated measurement tools in semiconductor manufacturing facilities to monitor wafer manufacturing schedules based on strict quality standards. In addition to silicon, an important material needed to make a CPU is metal. So far, aluminum has become the main metal material for making internal parts of processors, and copper has been gradually eliminated. There are some reasons. Under the current CPU operating voltage, the electromigration characteristics of aluminum are significantly better than copper.
The so-called electromigration problem means that when a large amount of electrons flow through a piece of conductor, the atom of the conductor substance is struck by electrons and leaves the original position, leaving a vacancy. If the vacancy is too large, the conductor connection is broken, and the atom leaving the position is removed. Staying in other locations can cause short circuits in other places and affect the logic function of the chip, which can make the chip unusable. This is why many Northwood PenTIum 4 are replaced with SNDS (Northwood Surgery Syndrome). When the enthusiasts first rushed to overclock the Northwood PenTIum 4, the chip electromechanical problem caused a serious electromigration problem. Hey. This is the first time intel has tried copper interconnect technology, and it clearly needs some improvement. On the other hand, the application of copper interconnect technology can reduce the chip area, and because the resistance of the copper conductor is lower, the current passing through it is also faster.
In addition to these two main materials, some kinds of chemical materials are needed in the design process of the chip, which play different roles and will not be described here.
Preparation stage for CPU manufacturing
After the collection of the necessary raw materials, some of these raw materials require some pre-treatment work. As the most important raw material, the processing of silicon is crucial. First, the silicon raw material is subjected to chemical purification, which is a step to achieve the level of raw materials available to the semiconductor industry. In order to make these silicon raw materials meet the processing needs of integrated circuit manufacturing, they must be shaped by melting the silicon raw material and then injecting the liquid silicon into the large high-temperature quartz container.
The blocks on the wafer are called "die," and each microprocessor becomes the "brain" of a personal computer system.
Then, the raw material is melted at a high temperature. We learned in the middle school chemistry class that many solid internal atoms are crystalline, as is silicon. In order to meet the requirements of high-performance processors, the entire silicon raw material must be highly pure, and monocrystalline silicon. The silicon raw material is then taken out from the high temperature vessel by means of rotational stretching, at which time a cylindrical ingot is produced.
From the current process, the diameter of the circular cross section of the ingot is 200 mm. But now intel and other companies have started using 300mm diameter silicon ingots. It is quite difficult to increase the cross-sectional area while retaining the various characteristics of the ingot, but as long as the company is willing to invest a large amount of money for research, it can be achieved. Intel's plant for the development and production of 300mm silicon ingots cost about $3.5 billion, and the success of new technologies has enabled intel to manufacture more complex and powerful integrated circuit chips. The 200mm silicon ingot plant also cost $1.5 billion. The following describes the manufacturing process of the CPU from the slicing of the silicon ingot.
Clean air flows continuously into the room from the gaps in the ceiling and floor. All air in the clean room is replaced many times per minute.
After making the ingot and ensuring it is an absolute cylinder, the next step is to slice the cylindrical ingot. The thinner the slice, the more material you use, the more processor chips you can produce. The slicing is also mirror finished to ensure that the surface is absolutely smooth and then checked for distortion or other problems. This step of quality inspection is particularly important, it directly determines the quality of the finished CPU.
The new slice is filled with something to make it a true semiconductor material, and then a transistor circuit representing various logic functions is scribed thereon. The doped substance atoms enter the gap between the silicon atoms, and an atomic force acts between them, so that the silicon raw material has semiconductor characteristics. Today's semiconductor manufacturing is dominated by CMOS processes (complementary metal oxide semiconductors).
The term complementary refers to the interaction between the N-type MOS transistor and the P-type MOS transistor in the semiconductor. N and P represent the negative electrode and the positive electrode, respectively, in the electronic process. In most cases, the slice is doped with a chemical to form a P-type substrate, and the logic circuit on which it is scribed is designed to follow the characteristics of the nMOS circuit. This type of transistor has higher space utilization and is more energy efficient. At the same time, in most cases, the appearance of pMOS transistors must be limited as much as possible, because in the later stages of the manufacturing process, N-type materials need to be implanted into the P-type substrate, and this process leads to the formation of pMOS transistors.
After the work of incorporating the chemical is completed, the standard section is completed. Then, each slice was placed in a high temperature furnace and heated to control the heating time to form a silicon dioxide film on the surface of the slice. The thickness of the silica layer is controllable by closely monitoring the temperature, air composition and warming time. In Intel's 90-nanometer manufacturing process, the gate oxide width is as small as an astonishing 5 atomic thickness. This layer of gate is also part of the transistor gate. The function of the transistor gate is to control the flow of electrons between them. By controlling the gate voltage, the flow of electrons is strictly controlled regardless of the voltage of the input and output ports.
The final step in the preparation is to cover the silicon dioxide layer with a photosensitive layer. This layer of material is used for other control applications in the same layer. This material has a good sensitizing effect when dried, and can be chemically dissolved and removed after the photolithography process is completed.
â— Photolithography
This is a very complicated process in the current CPU manufacturing process. Why is it said? The photolithography process uses a certain wavelength of light to inscribe the corresponding nick in the photosensitive layer, thereby changing the chemical properties of the material. . This technology requires extremely stringent wavelengths of light used, requiring the use of short-wavelength ultraviolet light and large curvature lenses. The etching process is also affected by stains on the wafer. Each step of etching is a complex and delicate process.
The amount of data required to design each step of the process can be measured in units of 10 GB, and the number of etching steps required to fabricate each processor exceeds 20 steps (one layer of etching per step). And if each layer of etched drawings is magnified many times, it can be even more complicated than the entire New York City plus suburban maps. Imagine reducing the entire New York map to a real area of ​​only 100 square millimeters. On the chip, then how complicated the structure of this chip is, you can imagine it.
When these etching operations are all completed, the wafer is flipped over. Short-wavelength light is transmitted through the hollow nicks on the quartz stencil onto the photosensitive layer of the wafer, and the light and stencil are removed. The photosensitive layer material exposed to the outside is chemically removed, and the silica is immediately formed below the hollowed out position.
Intel technicians monitor wafers in automated wet etch tools that remove excess processing aids or contaminants from the wafer.
â— Doping
After the residual photosensitive layer material is removed, the remaining is the filled silicon dioxide layer of the trench and the exposed silicon layer below the layer. After this step, another silicon dioxide layer is completed. Then, another polysilicon layer with a photosensitive layer is added. Polysilicon is another type of gate. Since a metal stock (hence the name metal oxide semiconductor) is used here, polysilicon allows the gate to be established before the transistor queue port voltage is active.
The photosensitive layer is also etched through the mask by short-wavelength light. After an etch, all the required gates are basically formed. Then, the exposed silicon layer is chemically bombarded by ion, and the purpose here is to generate an N-channel or a P-channel. This doping process creates all the transistors and circuit connections to each other. No transistor has an input and an output, and the two ends are called ports.
â— Repeat this process
From this point on, you will continue to add levels, add a layer of silicon dioxide, and lithography once. Repeat these steps, and then there is a multi-layered stereo architecture, which is the budding state of the processor you are currently using. Conductive connections between the layers are carried out using a metal coating technique between each layer. Today's P4 processor uses a 7-layer metal connection, while the Athlon64 uses 9 layers. The number of layers used depends on the original layout design and does not directly represent the performance difference of the final product.
â— Packaging test process
The next few weeks will require a turn-off test of the wafer, including testing the electrical characteristics of the wafer to see if there is a logic error, if so, at which level it appears. Then, each problematic chip unit on the wafer will be tested separately to determine if the chip has special processing needs.
The entire wafer is then diced into individual processor chip units. In the initial test, those units that failed the test will be abandoned. These chip units that are cut will be packaged in some way so that they can be smoothly inserted into the motherboard of a certain interface specification. Most intel and AMD processors are covered by a thermal layer.
After the completion of the finished processor, a full range of chip function tests are performed. This part will produce different grades of products. Some chips operate at a relatively high frequency, so the names and numbers of high-frequency products are marked, while those with relatively low operating frequencies are modified and other low-frequency models are applied. This is the processor for different market positioning. There are still some processors that may have some deficiencies in chip functionality. For example, if it has defects in the cache function (this kind of defect is enough to cause most CPUs), then they will be shielded from some cache capacity, which will reduce the performance and of course reduce the price of the product. This is Celeron. And the origin of Sempron.
After the CPU's packaging process is completed, many products have to be tested again to ensure that there is no omission in the previous manufacturing process, and that the product is completely compliant with the specifications without deviation.
KNM1L Series Moulded Case Circuit Breaker
KNM1L series Moulded Case Circuit Breaker is MCCB , How to select good Molded Case Circuit Breaker suppliers? Korlen electric is your first choice. All moulded Case Circuit Breakers pass the CE.CB.SEMKO.SIRIM etc. Certificates.
Moulded Case Circuit Breaker /MCCB can be used to distribute electric power and protect power equipment against overload and short-current, and can change the circuit and start motor infrequently. The application of Moulded Case Circuit Breaker /MCCB is industrial.
Korlen electric also provide Miniature Circuit Breaker /MCB. Residual Current Circuit Breaker /RCCB. RCBO. Led light and so on .
KNM1L series Molded Case Circuit Breaker,KNM1L series Small Size Molded Case Circuit Breaker,KNM1L series Electrical Molded Case Circuit Breaker,KNM1L series Automatic Molded Case Circuit Breaker
Wenzhou Korlen Electric Appliances Co., Ltd. , https://www.korlen-electric.com